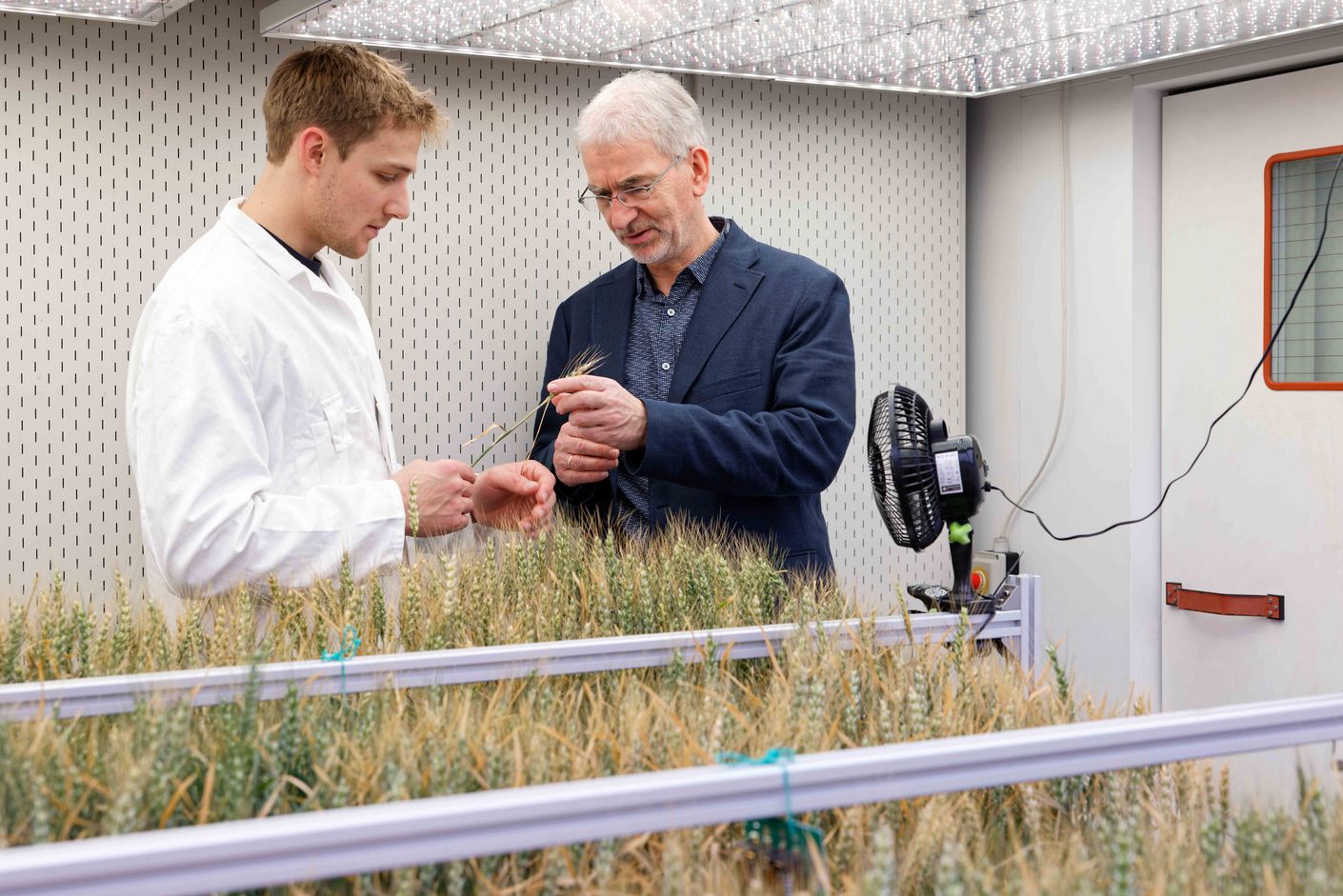
The grain revolution
Growing wheat and saving space: researchers in the WSS100 final project “Revolution of food production”, want to systematically drive the further development of vertical farming technologies forward to attain indoor harvests that are six thousand times larger than crop yields from conventional outdoor farms.
How can we feed the world’s growing population without depleting natural resources like water and soils—and destroying valuable ecosystems? This question is the research focus of the team led by Senthold Asseng at the Technical University of Munich. In their WSS100 proposal, they set out a concept for agricultural food production in a meticulously controlled environment—a radical expansion of today’s already existing vertical farming systems.
“Today’s vertical farms consume an enormous amount of energy and are extremely labour intensive, hence costly. If at all, cost-effective operations are only possible when growing premium leafy produce like lettuce and herbs,” Senthold Asseng explains. To make the indoor production of food staples such as wheat competitive, however, he says the entire system needs to be rethought, automated and made much more efficient. With this type of comprehensive approach, Asseng calculates that one hundred vertically stacked indoor planting fields with five to six harvests per year would yield up to six thousand times more wheat per square metre than outdoor farms.

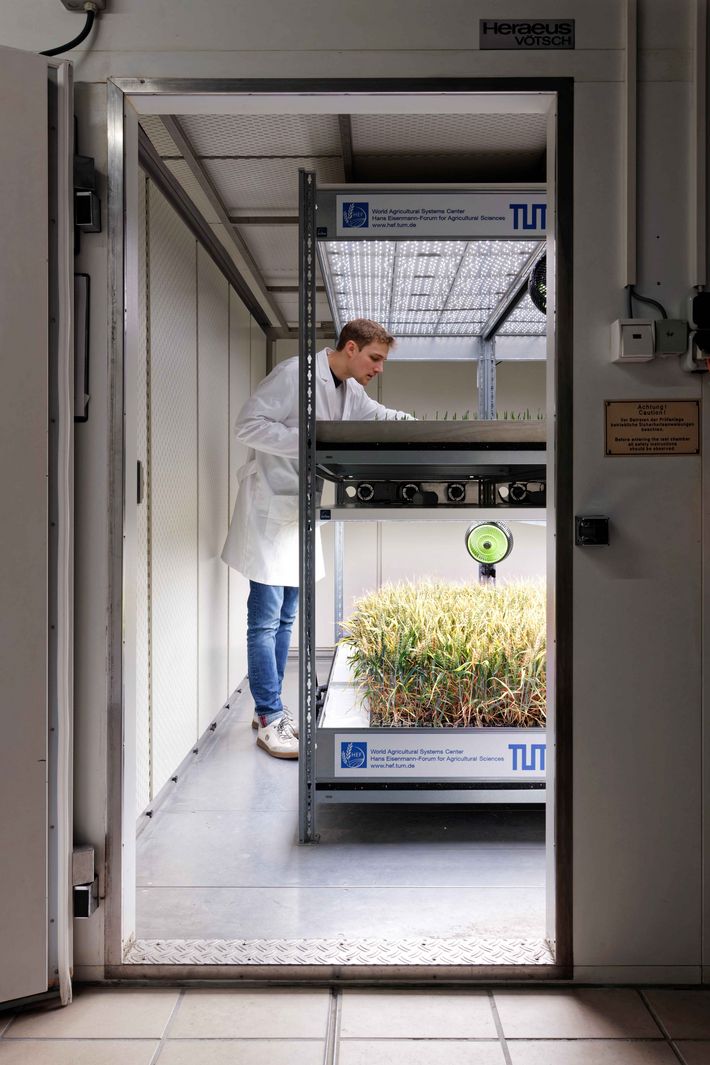
Large-grain dwarf wheat
To realise their innovative idea, every single aspect of vertical farming must be optimised—starting with the plants themselves. Wheat is the source of one-fifth of all calories consumed by humans and also the most extensively studied crop. To date, however, it has been cultivated for outdoor farming, rarely for a controlled environment. “Because temperature, light, humidity, fertilisers and all other factors are controlled in our system, we can reimagine how the plant should look,” Asseng says.
For example, the ideal wheat would be as short as possible, making it possible to stack numerous cultivation layers on top of each other in a production facility. “The height of wheat grown outdoors is instrumental in keeping weeds at bay,” Senthold Asseng says. “However, there won’t be any weeds in our facilities.” He and his team are already working with a wheat variety modified by the US space agency NASA in the 1990s for potential missions to Mars. Rather than being 1.1 metres high, like conventional, field-grown wheat, this variety measures just 50 centimetres. “But we want our wheat to be even shorter,” Asseng says.
Redesigning the wheat’s root system is another key aspect in the project. Whereas conventional wheat needs deep roots of up to two metres to absorb the necessary water and nutrients from the soil, an indoor variety that doesn’t have to work so hard to get what it needs would probably do well with roots of only ten centimetres, maybe even less, Asseng says. The energy the optimised plants save by not having to find their own nutrients can instead be invested into growing the grain.
Clever lighting
Just as important as cultivating the right wheat variety is identifying the conditions in which the plants thrive while using the least amount of energy possible. The researchers aren’t at a loss for new ways to achieve this aim, many of which are related to lighting, as it’s responsible for almost all of the energy costs in vertical farming. One option they’re testing is to reduce the light spectrum emitted in the facilities to only those wavelengths that the plants actually need to conduct photosynthesis. A fully automated conveyor could then move the light sources up and down so that they remain close to the plants at all times. “This is important, because light intensity, and consequently energy consumption, decreases by a power of two at this distance,” says Senthold Asseng, who wants to reduce energy use by ninety-three percent.
Another focus in the project is the principle of circularity. Highly efficient circulation systems will ensure that vertical farms function with ninety-five percent less water and sixty percent fewer fertilisers. Special wall coatings for dehumidification are one way of achieving this aim. Another is unused biomass broken down into minerals that can be utilised as fertiliser.
In barns and in the desert
To avoid wasting energy while also guaranteeing automated production systems, an optimised building is essential. The Munich team propose building the modular farm facilities of wood, an ecologically sustainable material choice. “The smallest unit will be five layers of planting space measuring ten by ten metres,” Asseng says. Thanks to their small size, the units could even be fitted into a barn at a conventional farm, where solar panels installed on the roof would supply the system with electricity. Large facilities with up to one hundred stacks would be used for large-scale food production—even in regions crops were previously unthinkable due to a lack of water, or because the soils are contaminated with heavy metals.
If we could grow high-quality wheat—and later other foods—without using up so much space, it would be a quantum leap for global food security. At the same time, it would also reduce the need for industrialised agriculture—all of which brings benefits to nature.
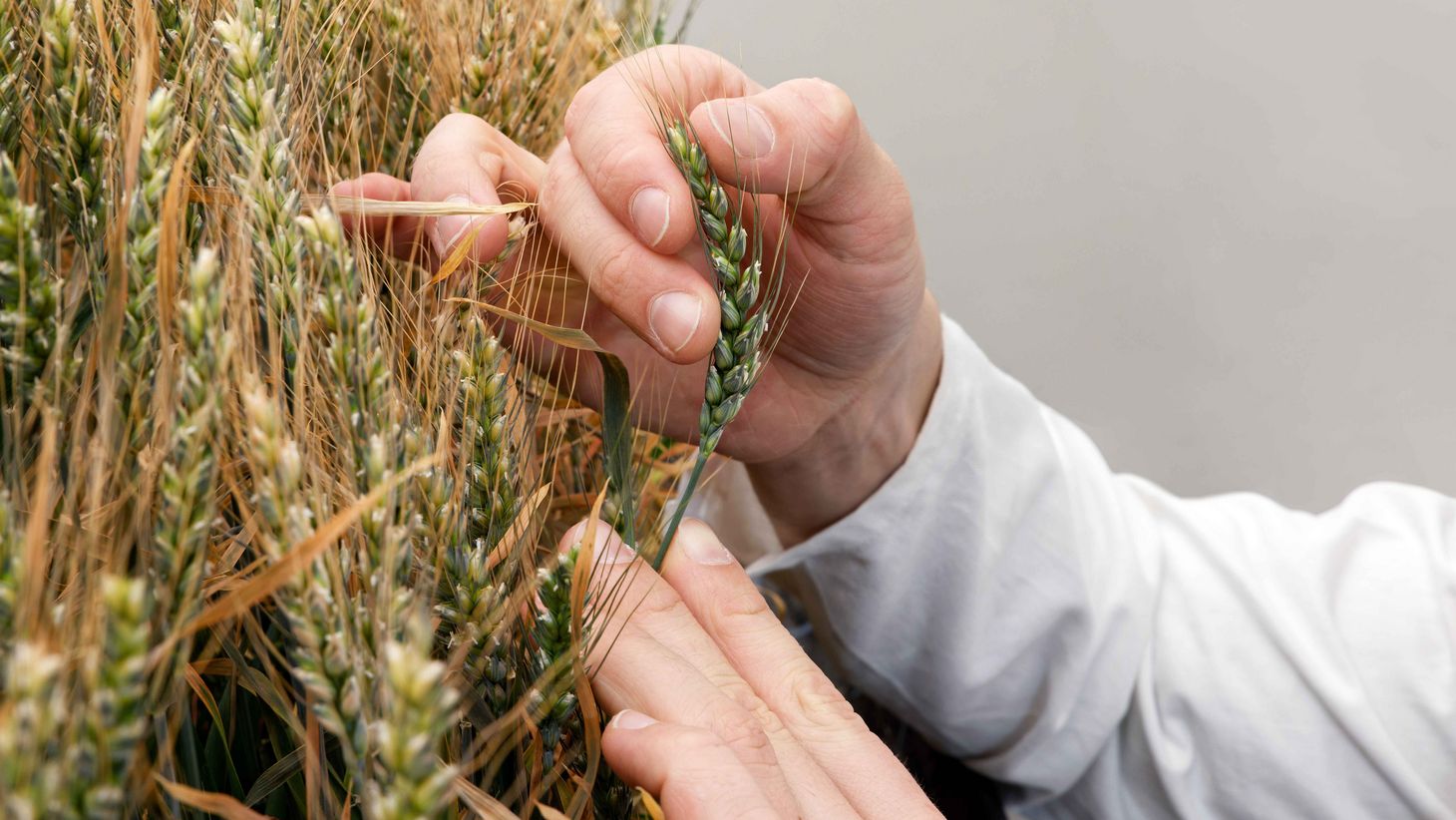
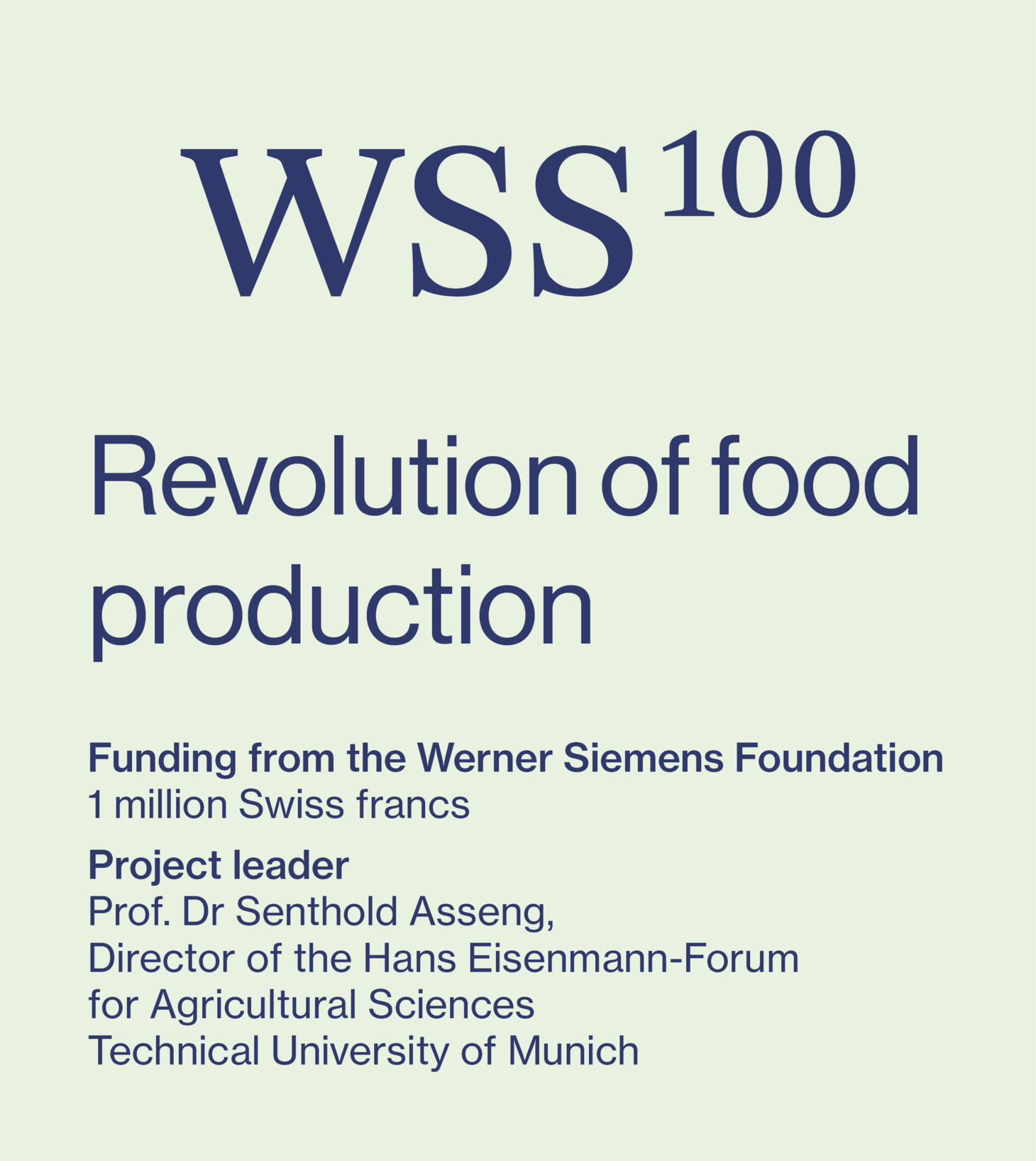